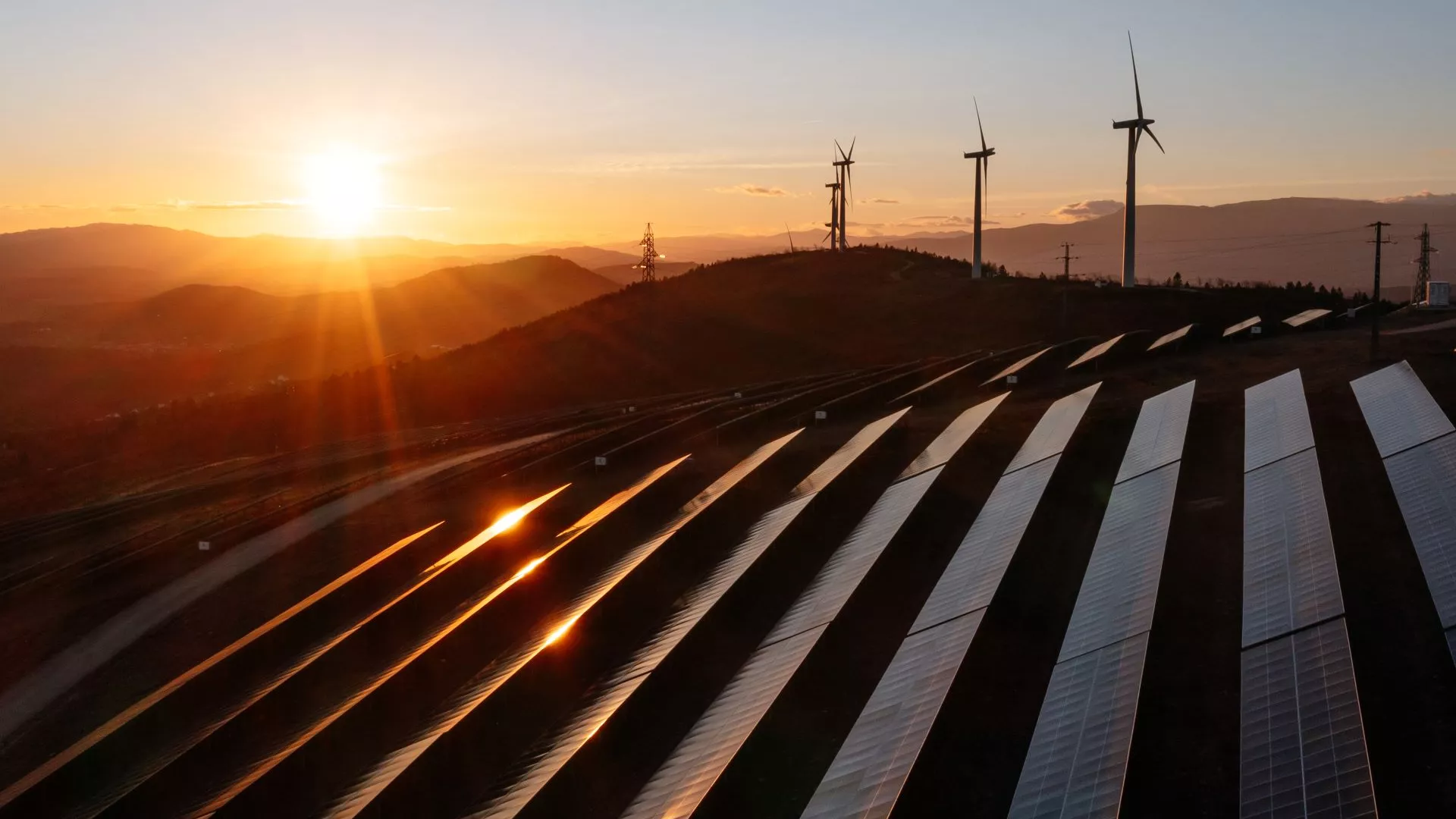
ODIN
What are the project’s objectives?
The main goal of the ODIN Project is to develop technology and new knowledge based on Digital Image Correlation (DIC) techniques to study the dynamic effects generated by electrotechnical equipment (generators, transformers, etc.), with a particular focus on the generation, transmission, and cancellation of vibrations, as well as the presence or absence of electrical voltage (energized equipment). This is achieved through safe, contactless methods using optical identification technology.
The project focused on research into industrial optics applications using Digital Image Correlation (DIC), particularly its photogrammetric variant, to identify dynamic parameters in electrotechnical systems within power generation and distribution environments. Contactless identification of such parameters is essential in this sector due to the potential for system interference and the inherently hazardous nature of the environment (high voltage, electric current, power, electromagnetic fields, etc.).
The project explored an industrial optical system using DIC capable of capturing mechanical variations (vibrations) and their harmonics, which are produced by alternating electric current at 50 Hz.
The initial project objectives were:
To develop technology and new knowledge regarding dynamic effects generated by electrotechnical equipment (generators, transformers, distribution systems, etc.), with a focus on vibration generation, transmission, and cancellation, as well as the presence or absence of electrical voltage (energized equipment).
To develop experimental laboratory-scale models to explore potential applications of this technology.
To transfer laboratory-level developments to real-world field applications, especially those related to industrial optics for detecting and resolving issues caused by dynamic (multiphysics) effects in electrical facilities.
To explore the feasibility of extending the proposed system to multiple plants, including its various functionalities and use cases (voltage control, predictive anomaly detection when signal patterns change significantly, noise, etc.).
During the project, a new objective emerged: the detection of electric fields using optical sensors, which expanded the project’s scope.
This project received funding from the Government of the Principality of Asturias through IDEPA and the Science, Technology and Innovation Plan (PCTI), as well as from the European Union through the European Regional Development Fund (ERDF).
What tasks have been carried out?
To meet the outlined objectives, a work plan was implemented from early 2020 to May 2022, summarized as follows:
Multiple working meetings involving EDP personnel and partner companies.
Definition of technical and functional requirements.
Proposal development for applications of interest.
Experimental modeling and laboratory testing.
Experimental modeling and field testing.
What were the project stages?
The main phases completed in the project include:
Identification of physical phenomena occurring in dynamic electrotechnical equipment, as well as a review of current industrial optical devices.
Definition of specifications and functional requirements.
Identification of mechanical wave sources using optical methods.
Development of potential applications for detecting energized equipment.
Construction of models using ANSYS MULTIPHYSICS.
Development of a test and validation plan at laboratory level.
Adaptation of experimental models for real-world application.
Deployment of the system in the field and testing for mechanical vibration detection and energized equipment identification.
What results have been achieved?
The project’s outcomes are summarized below:
Experimental protocols have been defined for detecting vibrations in electrotechnical equipment and for detecting electric fields using optical systems.
The necessary equipment for vibration and electric field detection has been specified.
Regarding vibration detection, successful results were obtained: differences between the project-developed system and commercial accelerometers did not exceed 5%.
As for identifying energized equipment, the developed system proved sensitive to the presence of electric fields, as its optical behavior changes in the presence of such fields.
Project funded by