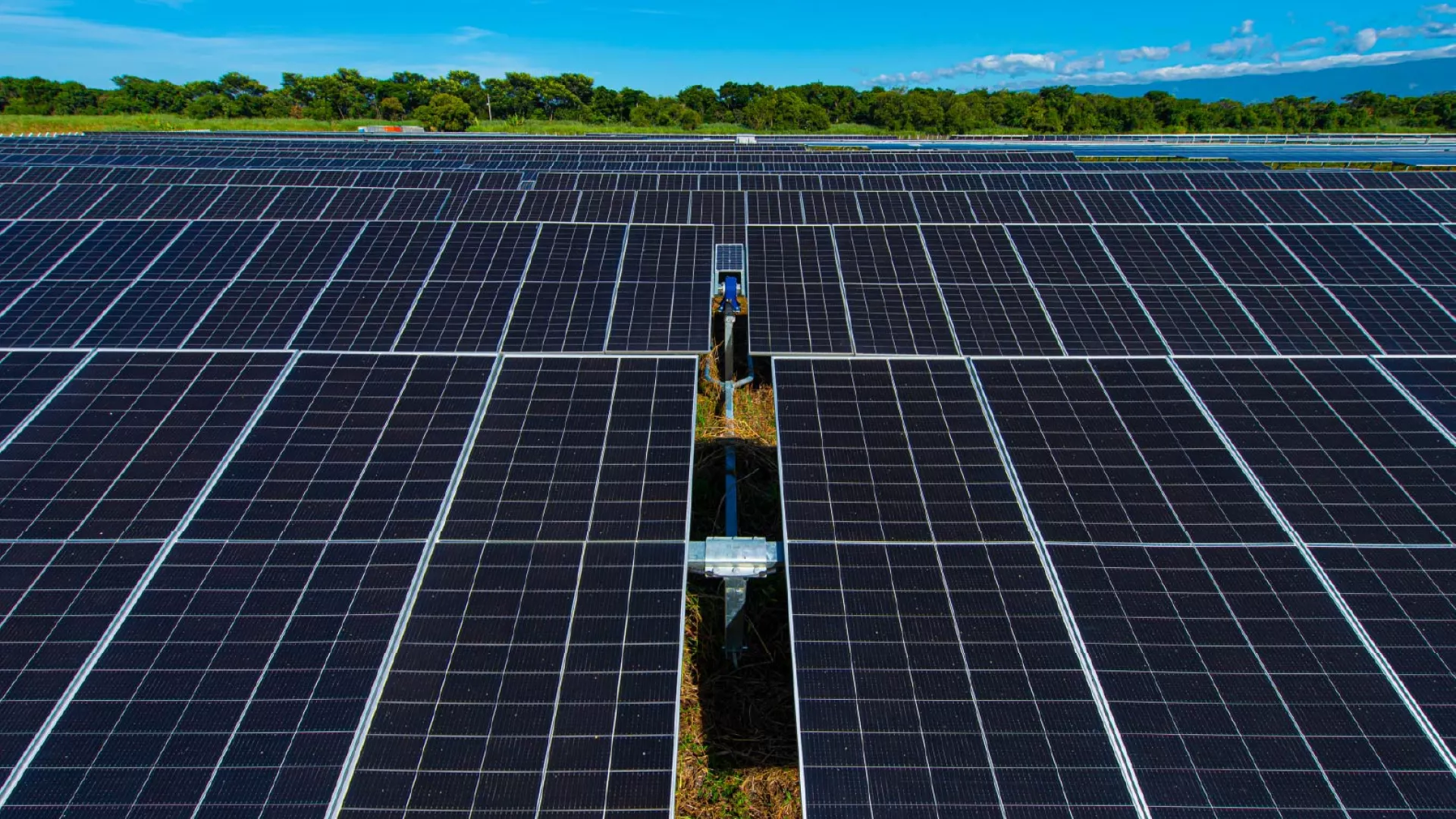
VASD
This project aims to carry out industrial research to acquire new knowledge that will enable the design of a new autonomous process for the maintenance of solar plants. As a result of the project, a prototype will be developed and validated in a relevant environment. To avoid the use of herbicides—which have a high environmental impact and incur significant costs when used continuously—the optimal alternative considered in this project is to study and design a device equipped with an autonomous navigation system and redundant sensors (visual and ultrasonic) that will allow it to safely navigate the solar installation while cutting and collecting vegetation without human intervention.
Therefore, the main objective of the project is to research technologies to perform the necessary vegetation control in large photovoltaic installations in a robotic and autonomous manner, with minimal emissions of dust and particles, and at a lower cost than current manual or manned operations.
To achieve this general goal, the following specific technical objectives have been defined:
Design and development of a cutting implement with biomass collection in a single pass, with estimation of the optimal working width and minimal emission of dust and particles.
Design and development of the robotic platform to handle the cutting and biomass collection implement, including calculation of optimal power.
Design and development of an autonomous robotic platform, with zero turning radius and high maneuverability.
Design and development of a robotic platform capable of autonomous operation regardless of weather and lighting conditions, including nighttime operation.
Design of an artificial vision and adaptive computing system, so that the developed prototype can detect obstacles and plan/replan its route.
System validation in a controlled environment.
System validation in an operational (field) environment (which corresponds to achieving a TRL 7 level).
To achieve the previously described objectives, a work plan was devised that extended from October 2021 to December 2023, and can be summarized as follows:
- Multiple work meetings of the project team, composed of EDP personnel and collaborating companies
- Analysis of requirements and specifications
- Definition and conceptual design of the system
- Technological research and component selection
- Conceptual design of clearing and collection implement
- Detailed engineering of clearing and collection implement
- Construction and assembly of clearing and collection implement
- Adjustments and commissioning of clearing and collection implement
- Study of the state of the art and selection of vision infrastructure in the domain
- Design of the interoperability layer between the global route planner and the local system
- Intelligent system for obstacle detection and route re-planning
- Integration with the robotic platform
- Adjustments, testing, and validation of the system
- Design and development of the communications subsystem
- Design and development of the control subsystem software
- Integration with the rest of the subsystems
- Adjustments, testing, and validation in controlled environment
- Adjustments and testing in relevant environment
- Analysis of results and research conclusions
The stages of the project are defined below:
- Strategic definition of the system
- Subsystem for clearing and collection
- Subsystem for guidance and obstacle detection
- Control subsystem
- Testing and validation